Approach to quality improvement from the customer’s point of view
LAPIS Semiconductor Co., Ltd.(Miyazaki Plant)is committed to quality and safety in order to deliver our reliable products from our customer’s point of view.
We adhere to the system and rules to fulfill our client’s requirement by the technology cultivated in the foundry business from customer’s perspective.
We provide a quick response to market changes and constantly improve the quality of our plants through continuous improvement.
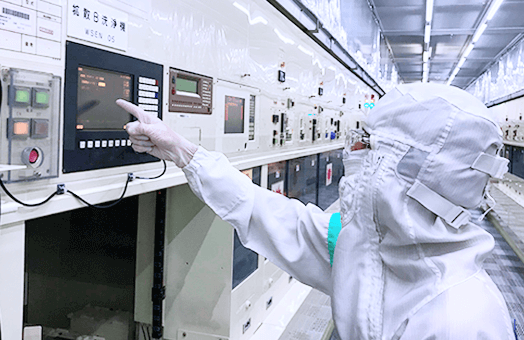
Improvement activities
Improvement activities to thoroughly pursue the root cause
LAPIS Semiconductor Co., Ltd.(Miyazaki Plant)have continuous improvement activities as part of our “Manufacturing innovation Activity”.
We started a new approach with the goal of “zero equipment failure” and “zero foreign material”.
We use this “Improvement Tools” to uncover the root causes and seek permanent measures for chronic problems such as “intermittent equipment failures” and “defective products due to foreign materials”.
We are working to develop human resources who can actively use this tool.
Almost half of all our engineers have acquired the “Improvement Tools” by 2018.
We have made further efforts to strengthen improvement by training instructors since 2019.
This effort will ensure that all engineers can utilize “Improvement Tools”.
Acquiring “Improvement Tools”
Learn logical and correct improvement methods.
We will develop human resources who can proactively carry out improvement activities through the best experience of practical training.
Method for management the risk equipment failures
Equipment troublers are caused by the collapse of the principle.
This method of restoring the collapse of the principle can eliminate equipment failures.
Approach method to zero foreign material
Foreign materials are not necessary to fulfill functions of products, however if they adhere to, stick to, or get inside the products, it will cause defects.
This method can eliminate defective products by understanding the true identity of the foreign materials, finding the generation process, analyzing the mechanism of defect occurrence, and taking countermeasure.
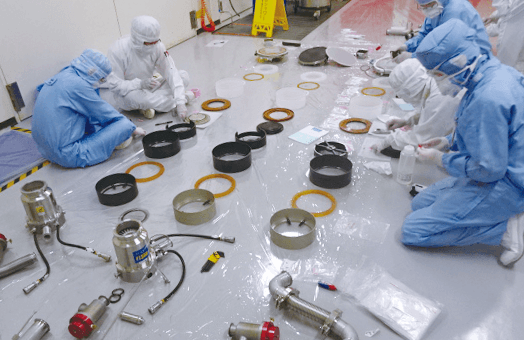
Training instructors
Engineers who have acquired the “Improvement Tools” will learn how to practice it, disseminate it within the company and instruct other engineers.
We aim to establish the same tools for our colleagues in our company and to continue the improvement activities quickly, accurately, efficiently and in a fun way.
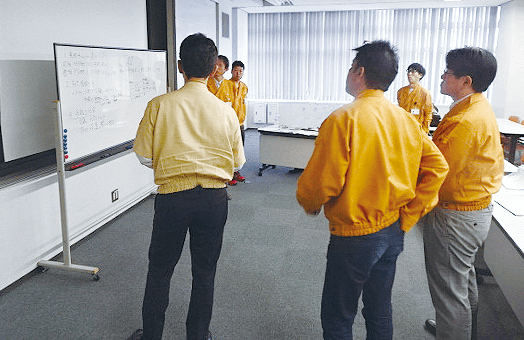